I’ve been hearing about “Constant Pressure Systems”; what does that mean? What do they do?
In the context of a residential water supply system, “Constant Pressure” refers to a combination of well, pump and control components designed to provide water to the home at a pressure that remains close to a chosen “set-point”, e.g. 60 psi, regardless of the amount of water (flow rate) being required at any one time.

A conventional design uses a pump, a tank with an air pre-charge in it, and a simple pressure operated switch. When the pump operates, it does so at its full rated power to drive water into the tank until the rising pressure causes the switch to shut it off. As you continue to use water, the pressure falls back down to the point where the switch turns the pump back on for another run cycle. This “pressure spread” is designed to be 20 psi. Tanks must be large enough to allow the pump to run for long enough to dissipate the heat in the motor generated by each startup (ideally about one minute).
A constant pressure system replaces the simple switch with a control (commonly called a Variable Frequency Drive, or VFD) and pressure sensor that together work to operate the well pump over a range of speeds, but always just fast enough to maintain that set-point pressure at the flow you happen to be using at the moment. All this is done electronically, in real time. Below is a video that goes over the basics of VFD’s.
Why is this better?
In a nutshell, you get a stable pressure in the house, without the up and down cycling you experience with a conventional system. Many water using devices are happier that way; your shower, for example, but especially in-ground irrigation systems. But that’s just the beginning.
VFD controlled pumps use a 3-phase motor design (think industrial strength) that is inherently more efficient than single phase motor/starter designs. The control starts the motor “softly” to avoid the shock and heat inherent in the “full-on” start of a cycling system. Even better, the strategy of running “just equal to the demand” uses less power overall that the start/stop scheme. The reasons are complicated (maybe for a later blog) but in a nutshell, less power = less heat; less heat = less waste and less strain and wear on equipment. The net result is lower operating cost and better reliability.
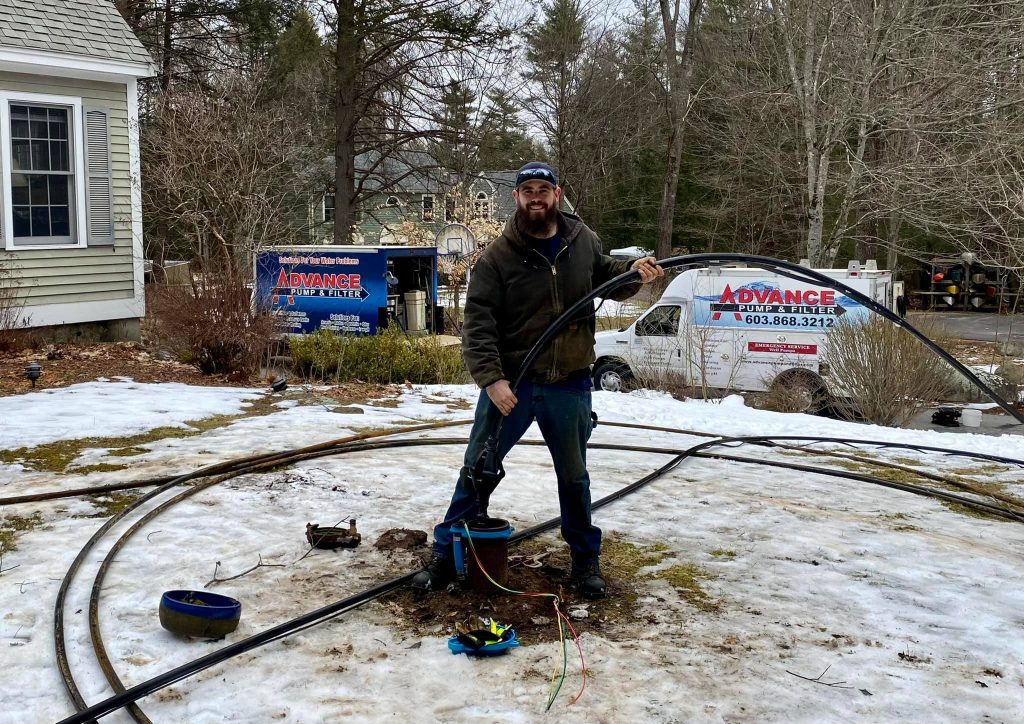
For more information about the benefits of constant pressure systems and whether it could be right for you, call us at 603-868-3212 or visit us online at http://www.advancepumpandfilter.com/nh_pump_filter_constant_pressure_systems.php